
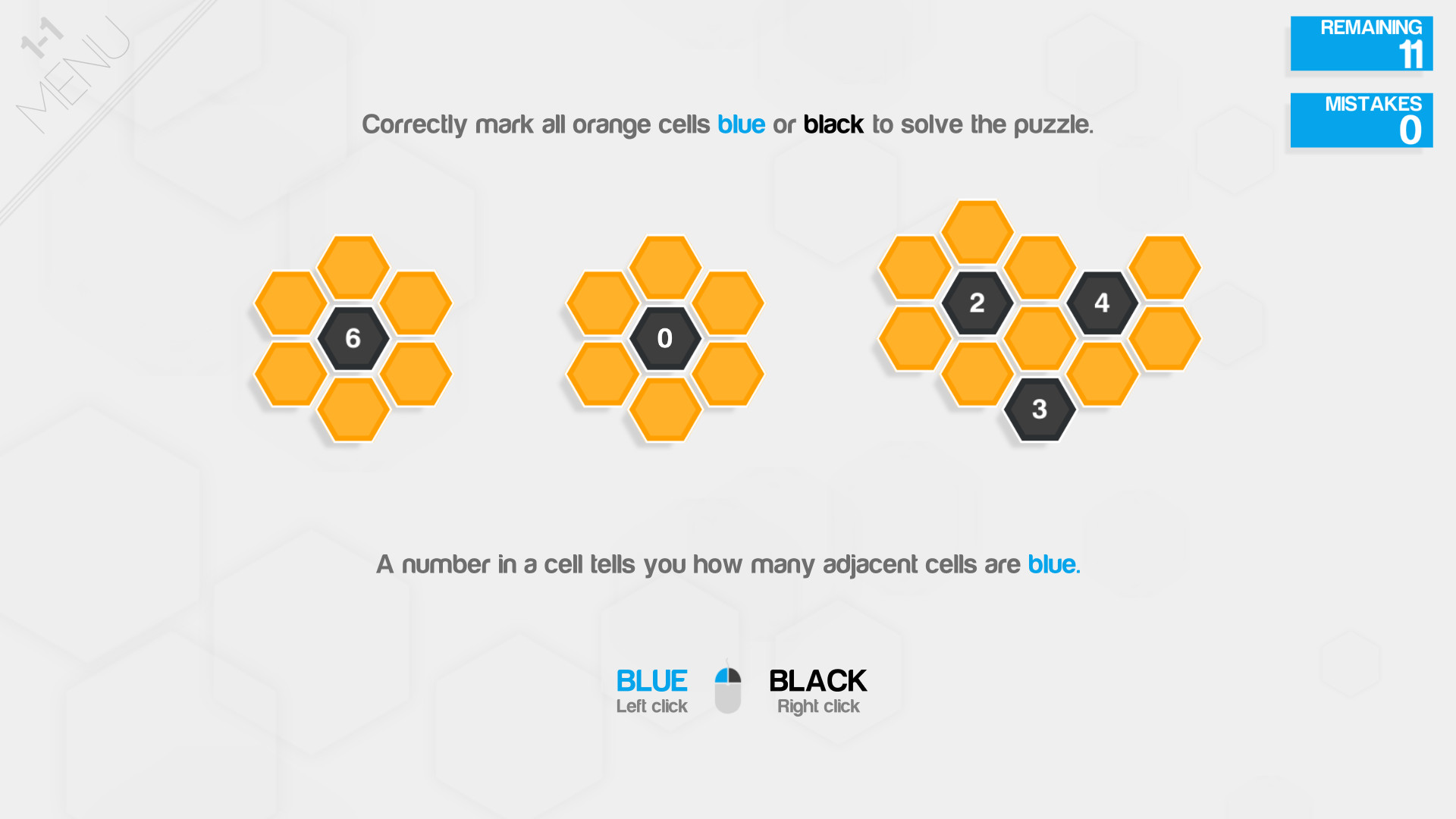

French M., Invention and Evolution: Design in Nature and Engineering, Cambridge Univ. Further insights are derived into the flow physics driving the aerodynamic efficiency benefits of smooth riblets, with riblets of height-to-spacing ratios of 0.5–0.8 identified as particularly promising in the case studies. The drag coefficient of ribleted airfoils is found to be mostly distributed around that of the bare airfoil, with the optimum being a favorable extreme point, thereby demonstrating the important role that adaptive-fidelity optimization plays in quickly identifying the (narrow) beneficial range of abstracted shape parameters. Substantial drag reduction of up to 17.2%, compared to the bare 3-D airfoil (without riblets), is achieved. The optimization process is integrated with open-source computer-aided design modeling, computational fluid dynamics, and postprocessing tools, with the provision for distributed batch processing, leading to a fully automated bioinspired design framework with potential for wider adoption. Given the prohibitive computational burden of simulating the surface flow at high fidelity around the submillimeter-scale riblets, an adaptive-fidelity design approach (namely, surrogate-based optimization with adaptive in situ model refinement) is adopted to enable tractable exploration of the hypothesized benefits of the new riblet concept. Unlike conventional riblet geometries (for example, sawtooth and scalloped shapes) overlaid on flat plates, the use of a new Gaussian-shaped abstraction overlaid on three-dimensional (3-D) airfoil surfaces is conceived in this paper. Bioinspired surface riblets have been known to improve drag performance by altering the near-wall flow structures, especially in the transitional flow regime.
